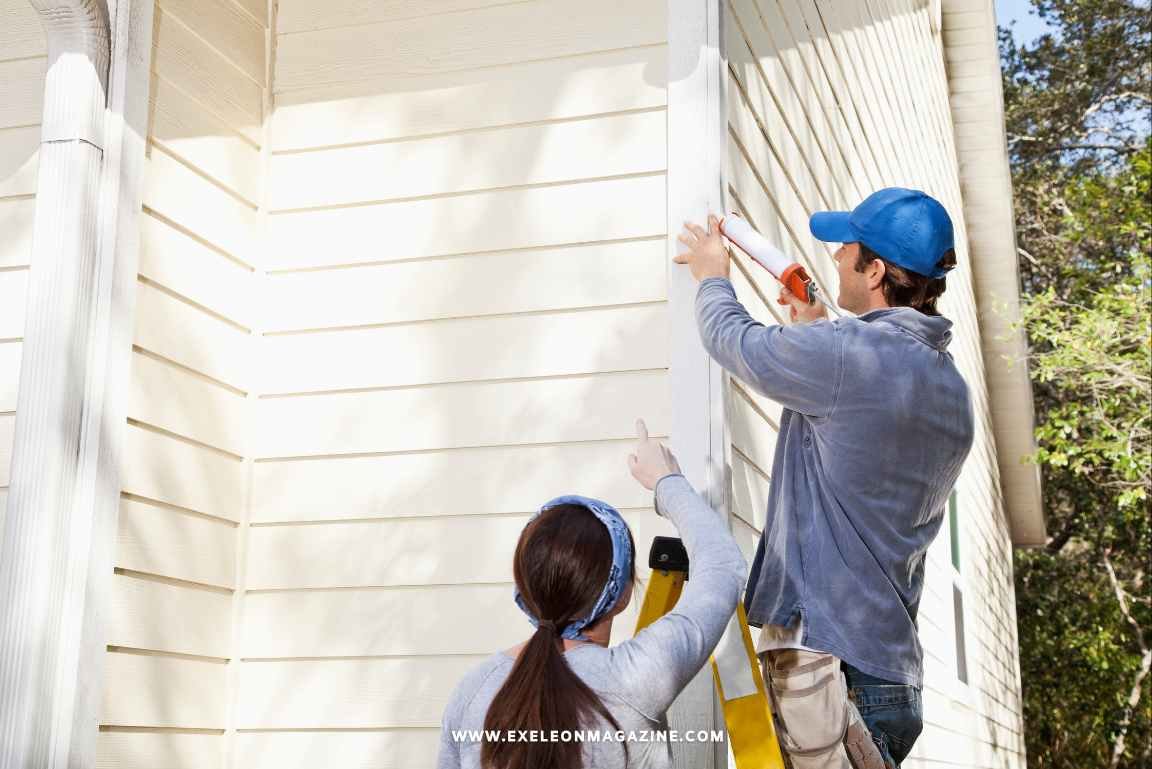
A lot of what keeps a home functional happens behind the scenes. The systems that provide water, heat, and backup support often sit silently in basements, closets, or underground. But just because they’re quiet doesn’t mean they’re problem-free. Tanks—whether they store oil, water, or chemicals—play a central role in keeping everything running. When they start to fail, the damage doesn’t always come with a warning. That’s why timely tank repair is a small move that prevents major disruptions.
Leaks, corrosion, or pressure issues inside a tank often begin subtly. There might be a slight odor, a barely noticeable drop in performance, or a change in fuel usage. Most homeowners miss these signs until the problem is big enough to demand immediate—and expensive—attention. Routine inspection and early repairs are the key to staying ahead of the curve.
Damage You Can’t Always See
Tank problems rarely start on the outside. Internal damage often happens slowly, caused by moisture, pressure changes, or chemical reactions inside the tank. If you’re using heating oil, even the quality of the fuel can accelerate wear. Once corrosion begins, it works from the inside out. By the time external damage is visible, the structural integrity may already be compromised.
This kind of hidden deterioration makes tanks especially risky to ignore. A sudden rupture or leak doesn’t just interrupt your system—it can cause environmental contamination, threaten your foundation, or spread damage to nearby equipment. Identifying and addressing these small failures early is what keeps your system safe and consistent.
Why Early Repairs Matter
Every tank has a lifespan, but that lifespan can be extended significantly with proper maintenance. Repairing small leaks, reinforcing weak seams, or replacing damaged fittings can add years to a tank’s usability. That’s especially important for larger or hard-to-replace tanks, such as those installed underground or as part of older heating systems.
Early tank repair also means you avoid emergency service fees, shutdowns during winter, or fuel waste. Once a tank starts leaking—even slowly—it’s already costing you money through reduced efficiency or lost product. And if you delay service too long, you might be forced into a full replacement, which is a much larger and more disruptive project.
Common Problems That Lead to Bigger Issues
Tanks deal with a lot—temperature fluctuations, pressure cycles, exposure to moisture, and chemical reactions from whatever they store. These stresses create weak points that develop over time. The most common issues include seam separation, valve failure, rusting interiors, and compromised welds.
Even simple misalignments or loose caps can allow air or contaminants into the system. That leads to sludge formation, condensation, or faster corrosion. These kinds of issues don’t fix themselves. They compound with use, especially in high-demand seasons like winter or summer when heating or irrigation systems are working overtime.
That’s why mid-cycle inspections and on-schedule tank repair are so effective. They catch these problems when they’re easy to fix, saving you from downtime or system failure later on.
Not All Repairs Are Equal
There’s a big difference between patching a leak and restoring structural integrity. Proper tank repair involves more than just stopping the immediate problem. Professionals assess the surrounding metal, fittings, and pressure response to make sure the damage hasn’t spread. They may recoat the interior, replace corroded hardware, or upgrade outdated parts to bring the tank up to modern standards.
Licensed repair technicians also ensure compliance with local codes and safety guidelines, which is especially important if your tank supports heating, plumbing, or fuel systems. DIY fixes or shortcuts may hold up temporarily but often fail under pressure—literally.
Preventing Future Disruptions
Once a tank fails, it’s rarely a single system that goes offline. Heating units, fuel pumps, plumbing fixtures, or emergency generators can all be affected. Keeping your tank in good condition isn’t just about avoiding leaks. It’s about preserving your entire system.
A repaired tank means steady fuel delivery, reliable water pressure, and no gaps in service when temperatures drop or storms roll in. It also protects the surrounding property. A leaking tank can seep into the foundation, create mold conditions, or compromise other structures nearby.
When to Call for Service
The best time to handle repairs is before you notice a full breakdown. If your tank is older than 15 years, has never been professionally inspected, or is showing changes in performance, it’s time for an evaluation. Some signs are subtle, like uneven heating, minor odors, or dampness near the tank site. Others are more serious, such as visible rust, sudden drops in pressure, or unusually high fuel consumption.
Even if the tank seems to be operating normally, don’t assume it’s fine. Internal rust or seal decay can develop without external symptoms. Regular checkups and quick responses to minor issues are what keep your system safe and operational year-round.