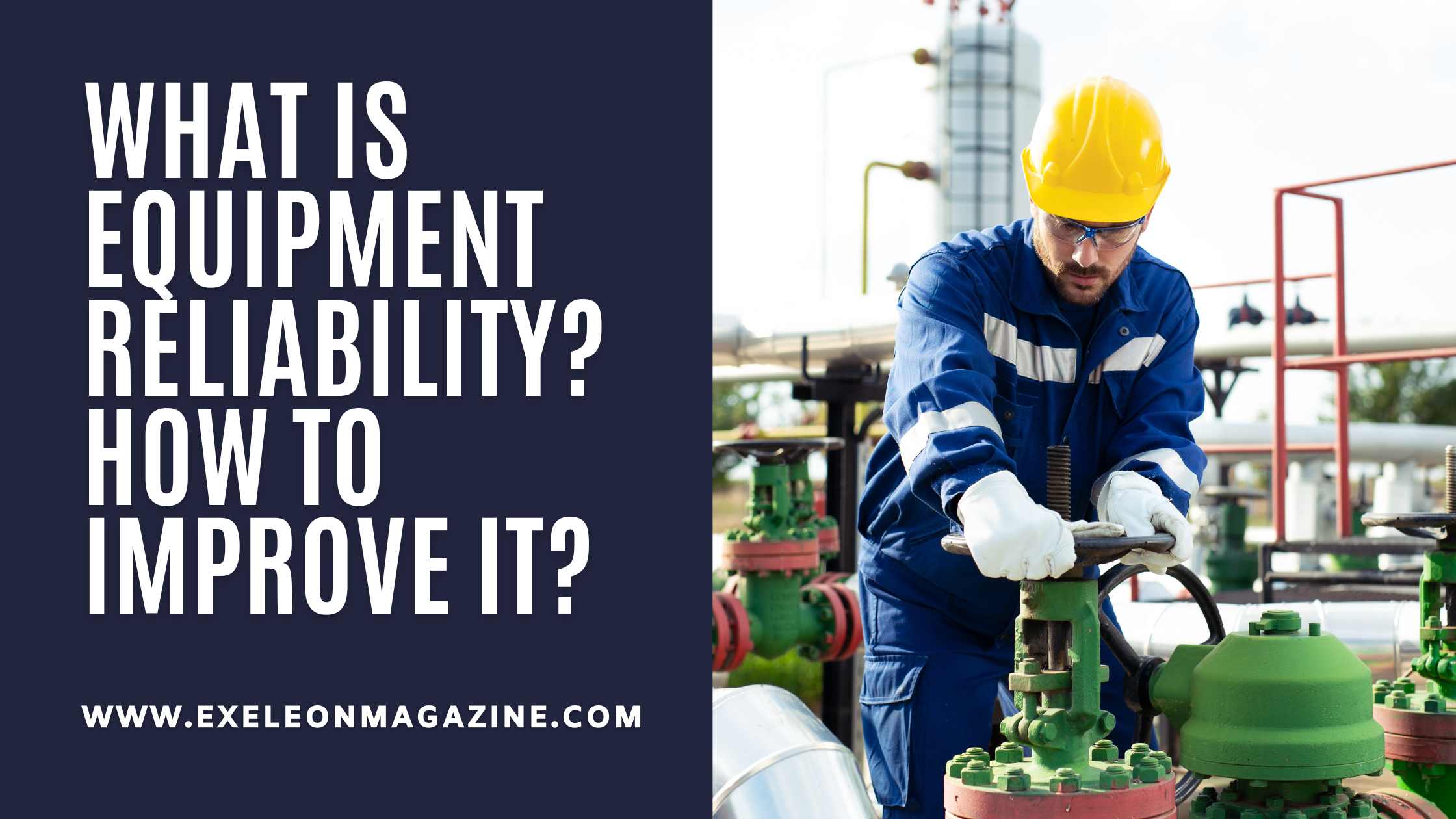
(ERM)(cn(((Businesses will get two significant gains thanks to Equipment Reliability upgrade procedures. To start, this method aids in keeping overhead to a minimum. Moreover, it ensures that the business can provide the goods and services that its customers need.
Making sure your projects are finished on time and within budget relies on the maintenance and reliability of your equipment. You may need to familiarize yourself with the word, so let’s start by defining it. Equipment reliability refers to how long an item can be expected to keep working well.
Reliability is vital to minimize safety concerns and financial losses on a building site with heavy equipment.
This article discusses equipment reliability, equipment reliability definition and offers few tips for improving it.
What Is Equipment Reliability?
The span of how equipment is expected to continue working well is a measure of its reliability. If it functions without breaking down, it is a good sign of its reliability.
To be reliable, equipment intended to last 9,000 hours must work as planned for at least 9,000 hours. Underperformance of equipment means maintenance and reliability metrics during runtime is shorter than specified. After this time, the reliability rating lowers to account for intermittent failure.
Unscheduled equipment breakdowns may be troublesome for businesses that need to be productive. To maximize productivity, you need an understanding of equipment maintenance.
What Is the Importance of Equipment reliability maintenance ERM?
Equipment reliability maintenance (ERM) boosts competitiveness. High-quality work comes from reliable equipment. ERM minimizes production costs by spending less on replacement parts and retooling.
There is less time and resources needed to make repairs. A significant improvement in preventing equipment failure is possible using a system to maximize ERM.
Industrial maintenance procedures decrease equipment failures, boost availability, and improve plant reliability. It guarantees that all plant assets are in good working condition.
Experts in the field of maintenance consulting have worked in various fields and enterprises. It allows them to advise their customers better on how to optimize their own operations. Maintenance consultants can be great assets to businesses that want to boost their productivity. Maintenance consulting with an outside expert will help firms get advice on how to improve their operations.
This is why plant maintenance is another name for industrial maintenance. Technicians in this field keep the plant’s equipment running smoothly by resolving any issue that might arise.
Their responsibilities include both proactive and reactive maintenance. Outside maintenance and reliability, contractors complete many tasks in companies. They are proficient in various tasks, such as repairing broken machines and doing other jobs as instructed.
Tips to Make Equipment More Reliable
1. Find Equipment Reliability Issues by Doing Root-Cause Analysis
It’s common for equipment to break down. Failures may be corrected with minimal harm and prevent devastating implications.
Breakdowns are frustrating for the operators and the company owners, and they might need to stop operations. Also, the price tag for unexpected downtime may add up quickly. Reports estimate that the annual losses of businesses are around 50 billion dollars due to unexpected problems.
Hence, it’s essential to get to the bottom of what’s causing the issue in the first place so that you can fix it and prevent it from occurring again.
For example, your excavator’s engine continually shuts down after being used for a while. It may be due to a clogged filter, a malfunctioning injection pump, or a fuel leak.
Finding the root of the problem is essential for finding a lasting solution. Using RCA to dig deeper to discover the causes is important.
The root-cause analysis helps operators and business owners to look at the larger picture at all times. When they tackle the causes of failure rather than simply the symptoms, they may finally end their costly repeated attempts to fix the issues.
Poor maintenance influences equipment reliability, but human error may be just as big a problem.
2. Invest in Operator Training
Properly trained personnel can use the equipment effectively and find the problems. Leaving your pricey equipment in the hands of an unskilled operator is like putting your baby in charge of making a five-course meal. The situation will be chaotic, which can lead to injuries and property damage.
Inexperienced operators stop equipment for minor problems, call for repairs, and halt production. Training is the better option to lessen repairs, shorten maintenance time, and prevent injuries.
3. Invest in Durable Low-Maintenance Equipment
There are ways to prepare for success even before you have the necessary tools. You should always consider the ease of maintenance when deciding to buy new equipment. The ease of operation may be gauged by inspecting the numerous access panels.
Parts availability is another factor to consider. Are there many one-of-a-kind specialty pieces, or are most of them relatively standard? Where do you stand on the issues of vendors?
How fast would you be able to acquire the parts? And how do you plan to handle the repairs you cannot do yourself? How long does it typically take to have an expert brought in? These may seem to be trivial, but they are important things to consider.
4. Make Use of Equipment Reliability Data
Modern technology lets us monitor our health, home activities, and corporate operations. Machines are just like everything else out there.
As a result, the popularity of using equipment data should be no surprise. Your can monitor your equipment’s location, health, and number of hours used with the correct software.
Having access to this information also facilitates more effective deployment of resources. It’s a handy tool for gauging whether or not a construction site has enough equipment to finish the construction.
Essential equipment may then be shipped from the closest location. Telematics is the use of remote monitoring systems to keep tabs on machinery. About 54% of construction businesses say telematics improves operator conduct.
5. Implement Cross-Training With Caution
Many believe that it’s a good idea to teach operators how to use different machines so that if one of them gets ill or quits, production will not suffer. While the concept is fantastic, it has yet to be fully realized.
The operator may remember six or seven things from cross-training. Equipment operators should be close and know things about them. Knowledgeable operators can minimize problems and optimize the machine’s capabilities with the help of others.
6. Put Security First
Consistency and security are inseparable aspects in maintenance. Maintain equipment by following regulations, hiring competent operators, and emphasizing worker safety. If the plant’s dependability is poor, operators might skip preventative maintenance.
When your operators gamble, they cause harm to themselves and their teammates. A safe workplace is the result of everyone’s effort. A piece of safety equipment is a trustworthy machine.
7. Make Use of Appropriate Methods of Upkeep
You are responsible for the repair of equipment once you own it. Which method of equipment reliability is most appropriate? Using many ways together will likely give the highest level of reliability.
It is like driving your vehicle. Through routine maintenance, you ensure that the parts are always in good condition. Several engine components need to be serviced, depending on their current state.
Old model cars lacked sensors but had temperature gauges to avoid engine damage. You have to refill the window washer fluid once it’s empty. Doing preventive maintenance means more uptime, less unexpected downtime, and lower expenditures.
These are the advantages, but there are also intangible ones. You reduce your stress level when you keep doing routine maintenance. When you know what to expect from your workplace, life improves.
8. Use Alerting Systems to Detect Faulty Equipment
A few noticeable signs may tell you whether your equipment is working properly, has problems, or needs a replacement. Statistical Process Control (SPC) can fine-tune equipment with little data.
You can save money on maintenance since you know if anything is wrong before it gets out of hand. By using SPC analysis, operators may decrease the number of accidents and costly repairs.
When it comes to equipment, the opinions of the management and workers often differ. Operators believe the management doesn’t listen to them, while the management believes they complain too often.
Operators want statistical help, so the management can solve problems with facts. The operators need to use the information they collect to resolve the issue.
9. Be Sure to Keep Your Equipment Clean
Dirt, oil, moist, and salt are some elements that can damage your tools at the job site. Dirt accumulation eventually harms your machinery and reduces its efficiency.
Although it’s tough, keeping equipment clean will improve its longevity and reliability. For example, dust on the electrical plugs can cause short circuits, which can be dangerous and inconvenient.
All of these problems may be prevented if you have a regular schedule of plug cleaning. Well-maintained and cleaned equipment often has a longer lifespan, is safer to use, and consumes less fuel.
Conclusion
Knowing how long a piece of machinery will be in working order in a certain period defines its dependability. The less likely your machinery will malfunction, the better its reliability.
Many options exist for bolstering dependability. One can determine the ease of maintenance and repair of new machinery before purchasing. Existing equipment from the same manufacturers might be tested for reliability as well.
Modern equipment maintenance software increases machine reliability. Using reliable data to make smart automation choices is one advantage.