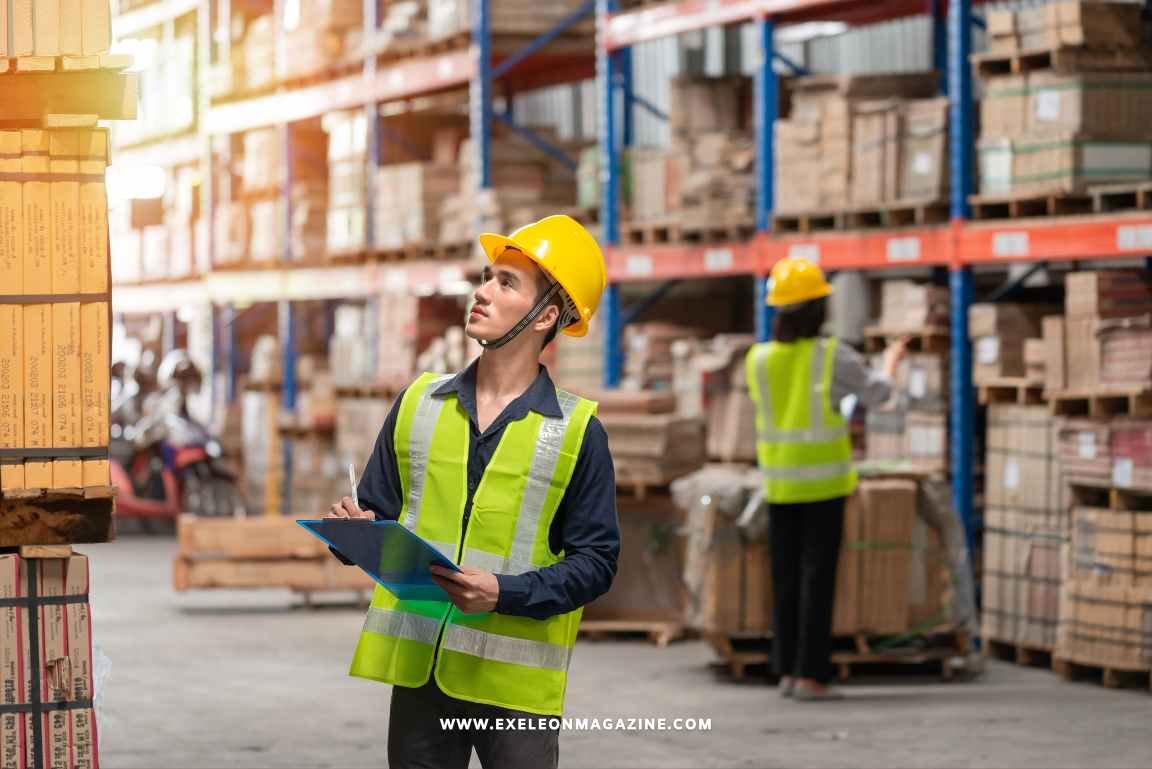
A Warehouse Management System (WMS) can significantly enhance warehouse operations by streamlining processes, reducing errors, and improving inventory accuracy. However, selecting the right WMS and overcoming the inherent challenges can be daunting. This guide aims to help you navigate these complexities, providing insights into the best methods for choosing a WMS and strategies to overcome common warehouse challenges
What is a Warehouse Management System (WMS)?
A Warehouse Management System (WMS) is a software solution designed to optimize warehouse operations. It manages inventory, tracks orders, and provides real-time visibility into warehouse activities. A WMS can automate many tasks, from receiving and putaway to picking and shipping, ultimately improving efficiency and reducing costs.
The Importance of a WMS
Implementing a WMS can transform your warehouse operations. Key benefits include:
- Improved Inventory Accuracy: Real-time tracking ensures accurate inventory levels, reducing the risk of stockouts or overstocking.
- Enhanced Efficiency: Automated processes streamline operations, allowing for faster order fulfillment and reduced labor costs.
- Better Customer Service: Accurate and timely order fulfillment leads to higher customer satisfaction.
- Scalability: A WMS can grow with your business, accommodating increased volume and complexity.
Selecting the Right WMS
Choosing the right WMS is critical for achieving the desired improvements in your warehouse operations. Here are some essential considerations:
1. Identify Your Needs
Before selecting a WMS, it’s important to understand your specific needs. Consider factors such as:
- Warehouse Size and Layout: The complexity of your warehouse layout and the volume of inventory will influence your WMS choice.
- Type of Products: The nature of your products, whether they are perishable, hazardous, or require special handling, will impact your WMS requirements.
- Order Volume and Complexity: High order volumes and complex order fulfillment processes necessitate advanced WMS features.
2. Evaluate Key Features
Look for a WMS that offers features aligned with your needs. Some of the best WMS features include:
- Real-Time Inventory Tracking: Provides visibility into stock levels and locations.
- Automated Picking and Packing: Reduces manual errors and speeds up order fulfillment.
- Integration Capabilities: Seamlessly integrates with your existing systems, such as ERP and CRM software. For instance, systems like SAP and Oracle offer robust integration options.
- Scalability: Can grow with your business and handle increased complexity.
WMS and Inventory Management >>
3. Consider Customization Options
Every warehouse is unique, and a one-size-fits-all approach may not work. Look for WMS customization options to tailor the system to your specific needs. Customizable workflows, user interfaces, and reporting tools can significantly enhance the usability and effectiveness of the WMS.
4. Conduct a Cost-Benefit Analysis
While the initial investment in a WMS can be substantial, it’s essential to conduct a cost-benefit analysis of WMS to determine the long-term value. Consider factors such as:
- Initial Implementation Costs: Hardware, software, and setup costs.
- Ongoing Maintenance and Support: Fees for software updates, technical support, and training.
- Operational Savings: Labor cost reductions, improved accuracy, and faster order fulfillment.
5. Vendor Reputation and Support
Select a reputable WMS vendor with a proven track record in your industry. Consider the level of support offered, including training, technical assistance, and user communities. Good vendor support can make a significant difference in the successful implementation and ongoing use of the WMS.
Overcoming Warehouse Challenges with a WMS
Even with the best WMS, warehouses can face various challenges. Here are common challenges and how a WMS can help overcome them:
1. Inventory Management
- Challenge: Inaccurate inventory counts can lead to stockouts or overstocking, affecting order fulfillment and customer satisfaction.
- Solution: A WMS provides real-time inventory tracking, ensuring accurate inventory levels and reducing discrepancies. Automated cycle counting and barcode scanning improve accuracy and efficiency.
2. Order Accuracy and Fulfillment
- Challenge: Manual processes can result in picking errors, delayed shipments, and dissatisfied customers.
- Solution: Automated picking and packing features in a WMS reduce errors and speed up order fulfillment. Real-time order tracking allows for better communication with customers regarding order status.
3. Space Utilization
- Challenge: Poor warehouse layout and space utilization can lead to inefficiencies and increased operational costs.
- Solution: A WMS helps optimize warehouse layout by analyzing product placement and movement patterns. It can suggest the best locations for inventory, improving space utilization and reducing travel time for picking.
4. Labor Management
- Challenge: Managing a large workforce and ensuring productivity can be challenging, especially in high-volume warehouses.
- Solution: A WMS provides labor management tools to track employee performance, assign tasks, and optimize workforce allocation. Automated task assignments ensure efficient use of labor resources.
5. Integration with Other Systems
- Challenge: Disconnected systems can lead to data silos and inefficiencies in warehouse operations.
- Solution: A WMS with strong integration capabilities ensures seamless communication between different systems, such as ERP and CRM. For example, integrating with ERP systems like MS Dynamics or Infor can streamline data flow and improve overall efficiency.
6. Adapting to Changing Business Needs
- Challenge: As businesses grow and evolve, their warehouse operations must adapt to new challenges and increased complexity.
- Solution: A scalable and customizable WMS can grow with your business. Regular software updates and flexible customization options ensure the system remains relevant and effective.
The Role of Automated Warehouse Systems
Automated warehouse systems are revolutionizing warehouse management. These systems use advanced technologies, such as robotics and artificial intelligence, to automate various warehouse tasks. The benefits of automated warehouse systems include:
- Increased Efficiency: Automation reduces the time and labor required for tasks such as picking, packing, and sorting.
- Improved Accuracy: Automated systems minimize human errors, ensuring higher accuracy in inventory management and order fulfillment.
- Cost Savings: Although the initial investment can be high, automated systems can lead to significant cost savings in the long run by reducing labor costs and increasing productivity.
Implementing Automated Systems
When considering automated warehouse systems, it’s essential to:
- Assess Your Needs: Determine which tasks can be automated and the potential benefits.
- Choose the Right Technology: Select automation technologies that align with your warehouse operations.
- Plan for Integration: Ensure that automated systems can integrate with your existing WMS and other systems.
- Train Your Workforce: Provide training to employees to effectively operate and maintain automated systems.
Improving Warehouse Operations
A WMS is a powerful tool for improving warehouse operations. Here are some strategies to maximize its benefits:
1. Continuous Improvement
Regularly review and analyze warehouse performance data to identify areas for improvement. Use the insights provided by the WMS to make data-driven decisions and implement changes that enhance efficiency and productivity.
2. Employee Training and Engagement
Invest in training programs to ensure employees are proficient in using the WMS. Encourage feedback and involve employees in process improvement initiatives. Engaged and well-trained employees are more likely to adopt new technologies and contribute to operational success.
3. Leverage Advanced Features
Take full advantage of advanced WMS features, such as predictive analytics, automated reporting, and real-time dashboards. These features can provide valuable insights into warehouse performance and help you make informed decisions.
4. Regular Maintenance and Updates
Keep your WMS up to date with regular maintenance and software updates. This ensures the system remains secure, efficient, and capable of handling new challenges as they arise.
5. Collaborate with Vendors
Maintain a strong relationship with your WMS vendor. Collaborate on system enhancements, seek support when needed, and participate in user communities to stay informed about best practices and new features.
Conclusion
Choosing the right Warehouse Management System (WMS) and overcoming warehouse challenges are critical steps toward optimizing your warehouse operations. By carefully selecting a WMS that meets your specific needs, leveraging automation technologies, and continuously improving your processes, you can achieve significant gains in efficiency, accuracy, and customer satisfaction.
Investing in a WMS and automated warehouse systems is a strategic decision that can deliver substantial long-term benefits. Conduct a thorough cost-benefit analysis of WMS, consider customization options, and prioritize integration capabilities with ERP systems like SAP and Oracle to maximize the value of your investment. By addressing common warehouse challenges with the right solutions, you can transform your warehouse into a competitive advantage for your business.
You May Also Like: