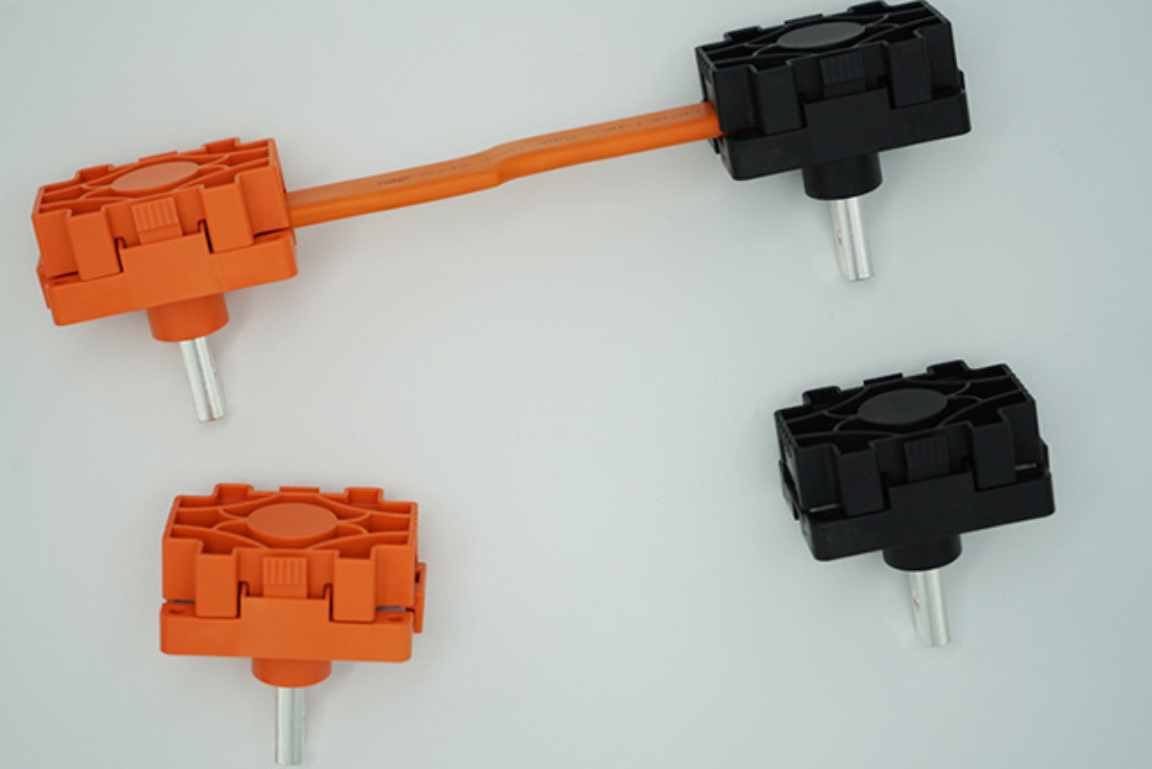
Bus bar connectors are the unsung heroes of electrical systems, providing a path for current, ensuring stability and efficiency in a range of applications. But like any other component, they can run into issues over time. Addressing these problems promptly is key to keeping your system running smoothly.
Let’s explore common problems and learn how you can diagnose and prevent them effectively.
Loose connections
Loose connections are one of the most frequent faults you’ll encounter, leading to intermittent operation, increased resistance, and even electrical arcing – a serious fire hazard. You can use a torque wrench to check bolts or fasteners are tightened to manufacturer specifications.
You should inspect connections periodically, especially in systems subject to vibration. Locking washers or thread-locking compounds can also help maintain secure fits over time.
Overheating
Overheating may damage these components and compromise their conductivity. It usually results from excessive current, poor ventilation, or degraded insulation. Telltale signs include melted insulation or a burned smell near the connectors.
To troubleshoot, measure the operating temperature with a temperature sensor. If you find a hot spot, check the load current doesn’t exceed the bus bar’s rating.
Additionally, inspect the surrounding environment for proper ventilation, and always calculate the anticipated load to select bus bar connectors with adequate current-carrying capacity. Regularly removing dust and debris also helps improve heat dissipation.
Corrosion
Corrosion weakens connectors and increases electrical resistance, reducing efficiency and causing localized heating. Exposure to moisture, salt, or chemicals is often to blame. Look for green or white deposits or flaking material on the connector surface.
To address it, disconnect power then clean the affected area with a non-abrasive brush or cloth and apply a protective anti-corrosion coating. For severe cases, you’ll need to replace the connector.
Misalignment
Misaligned parts create mechanical stress and uneven contact, leading to reduced efficiency and potential failure. It often results from improper installation or structural shifts in the system.
Inspect the connectors to make sure they align well with their counterparts. If needed, loosen and realign them to the proper position before re-tightening. Always use alignment guides or templates and ensure the mounting surface is level and stable.
Wear
Wear and tear is inevitable, especially in systems with frequent disassembly or high vibration. Signs include worn-down contact surfaces, cracks, or degraded insulation.
When you detect it, replace the damaged connector right away to avoid further issues. To minimize degradation over time, use components made of durable materials such as copper or aluminum and ensure they’re installed in low-vibration environments. Avoiding unnecessary disconnection and reconnection can also extend their lifespan.
Bus bar components are vital for your system’s performance. With a diligent approach, yours will keep powering your operations reliably for years to come.