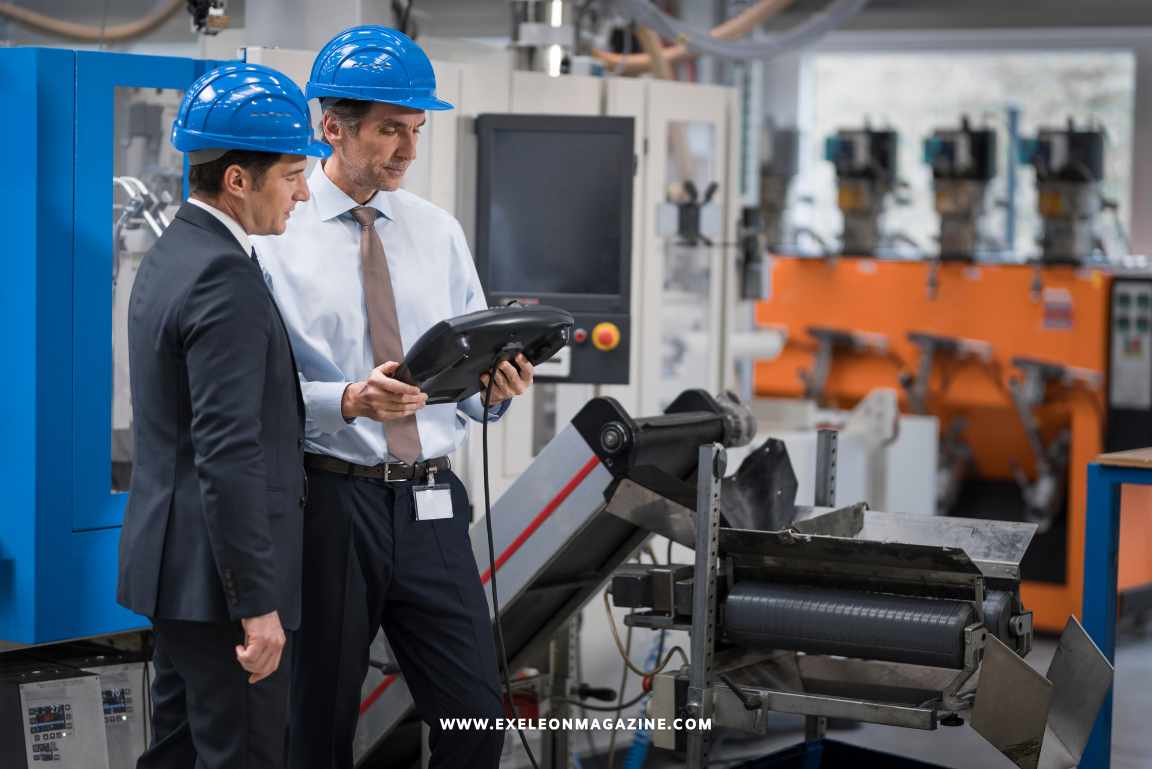
Industrial operations are the backbone of any manufacturing process. Efficiency in these operations directly translates to better productivity, cost savings, and improved safety. In an ever-competitive market, streamlining these processes can give a business the edge it needs to stay ahead. Let’s delve into the best methods for achieving streamlined industrial operations.
Assessing Current Operations
The first step in streamlining industrial operations is conducting a comprehensive audit of the current processes. Understanding where inefficiencies lie is crucial. Are there bottlenecks that slow down production? Are resources being wasted? By thoroughly assessing these aspects, companies can set clear, achievable goals for improvement. This assessment isn’t just about identifying problems—it’s about discovering opportunities for enhancement.
An audit should involve key stakeholders from all levels of the organization to get a complete picture of the operation. Using tools like value stream mapping can help visualize the flow of materials and information. Once the audit is complete, prioritize areas for improvement based on their impact on the overall operation. Setting measurable goals is essential for tracking progress and ensuring that efforts are aligned with the company’s strategic objectives. Regular reassessments should be scheduled to maintain continuous improvement.
Implementing Automation and Technology
Automation and technology have revolutionized industrial operations. With the advent of the Internet of Things (IoT) and Artificial Intelligence (AI), there are now more tools than ever to increase efficiency. Automation tools and software can handle repetitive tasks, reducing the likelihood of human error and freeing up workers for more complex responsibilities. For example, a case study showed that a mid-sized manufacturing plant reduced its production time by 30% after implementing robotic automation. These technologies not only boost productivity but also provide valuable data insights for continuous improvement.
Moreover, integrating smart sensors can enhance predictive maintenance, preventing costly downtime. Robotics can be programmed to operate around the clock, increasing throughput without additional labor costs. AI algorithms can analyze production data to optimize workflows in real time. Cloud-based solutions enable remote monitoring and control, offering flexibility and responsiveness. By embracing these technologies, companies can create more agile and responsive industrial environments.
Optimizing Material Handling
Material handling is a critical component of any industrial operation. Efficient material handling systems can significantly enhance productivity. Advanced equipment like robotic arms and automated guided vehicles (AGVs) play a crucial role in this optimization. Consider using self-dumping hoppers, for instance. These hoppers streamline the disposal of scrap materials, reducing manual handling and improving safety. Integrating self-dumping hoppers into existing workflows can lead to faster material movement and reduced labor costs. Additionally, optimizing layout design can minimize travel distances for materials and workers. Implementing conveyor systems can automate material transfer between workstations. Regular maintenance of material handling equipment ensures reliability and reduces the risk of breakdowns. Training employees on proper usage and handling techniques is essential for maximizing efficiency. Leveraging advanced tracking systems can provide real-time visibility of material flow, further enhancing operational efficiency.
Enhancing Workforce Training and Safety
A skilled workforce is essential for streamlined operations. Investing in training programs not only improves worker skills but also boosts morale and job satisfaction. Safety is another crucial aspect. Industrial environments can be hazardous, and implementing stringent safety protocols is necessary to reduce workplace accidents. Providing regular safety training and ensuring that all employees are aware of the latest safety standards can create a safer, more productive work environment.
Comprehensive onboarding programs for new hires can quickly bring them up to speed on operational standards. Cross-training employees can provide flexibility in workforce allocation. Investing in ergonomic equipment can reduce the risk of injury and enhance worker comfort. Regular safety drills and audits help reinforce a culture of safety. Encouraging open communication about safety concerns ensures that issues are addressed promptly and effectively.
Adopting Lean Manufacturing Principles
Lean manufacturing principles focus on waste reduction and continuous improvement. These principles are fundamental to streamlining operations. By adopting practices such as just-in-time production and continuous improvement, companies can reduce waste and enhance efficiency. For instance, Toyota’s implementation of lean manufacturing has been widely regarded as a benchmark in the industry. Practical steps to implement lean manufacturing include identifying value streams, mapping out the production process, and continuously seeking areas for improvement. Implementing 5S (Sort, Set in order, Shine, Standardize, Sustain) can create a more organized and efficient workplace.
Using Kanban systems can optimize inventory levels and production scheduling. Involving employees in problem-solving activities can harness their insights and foster a culture of improvement. Lean Six Sigma techniques can further enhance process efficiency and quality. Regularly reviewing and refining lean practices ensures they remain effective and aligned with business goals.
Improving Supply Chain Management
A streamlined supply chain is vital for efficient industrial operations. By optimizing supply chain processes, companies can ensure a smoother flow of materials and reduce delays. Building strong relationships with suppliers is key to achieving this. Utilizing supply chain management software can provide better visibility and control over the entire supply chain. This software helps in tracking inventory levels, managing orders, and forecasting demand, leading to improved planning and reduced disruptions. Collaborative planning with suppliers can align production schedules and inventory levels.
Implementing just-in-time delivery reduces inventory holding costs and improves cash flow. Advanced analytics can optimize supplier selection and performance evaluation. Digital twins can simulate supply chain scenarios to identify potential bottlenecks and test mitigation strategies. By fostering a collaborative and transparent supply chain, companies can enhance resilience and responsiveness.
Monitoring and Continuous Improvement
Regular monitoring and assessment are crucial for sustaining streamlined operations. Tools and techniques such as Key Performance Indicators (KPIs) and Six Sigma methodologies can help in tracking performance. Encouraging a culture of continuous improvement is essential. Employees should be motivated to suggest improvements and be actively involved in the process. Continuous improvement is not a one-time effort but a persistent approach to enhance every aspect of the operations. Implementing a structured problem-solving framework like PDCA (Plan-Do-Check-Act) ensures systematic improvement. Regularly reviewing KPIs keeps the focus on critical performance areas. Conducting root cause analysis helps identify underlying issues and prevent recurrence. Celebrating small wins can boost morale and maintain momentum. By embedding continuous improvement into the organizational culture, companies can achieve sustainable long-term success.
Conclusion
Streamlining industrial operations involves a combination of thorough assessment, technological adoption, skilled workforce training, lean principles, efficient supply chain management, and continuous monitoring. Each of these methods plays a vital role in enhancing productivity and reducing costs. The journey towards streamlined operations may seem daunting, but the benefits far outweigh the challenges. By implementing these strategies, companies can achieve a competitive edge and drive long-term success. Are you ready to take the first step toward streamlined operations? Start today by assessing your current processes and identifying areas for improvement. The future of your business depends on the efficiency of your operations. The time to act is now—don’t let inefficiencies hold your business back.