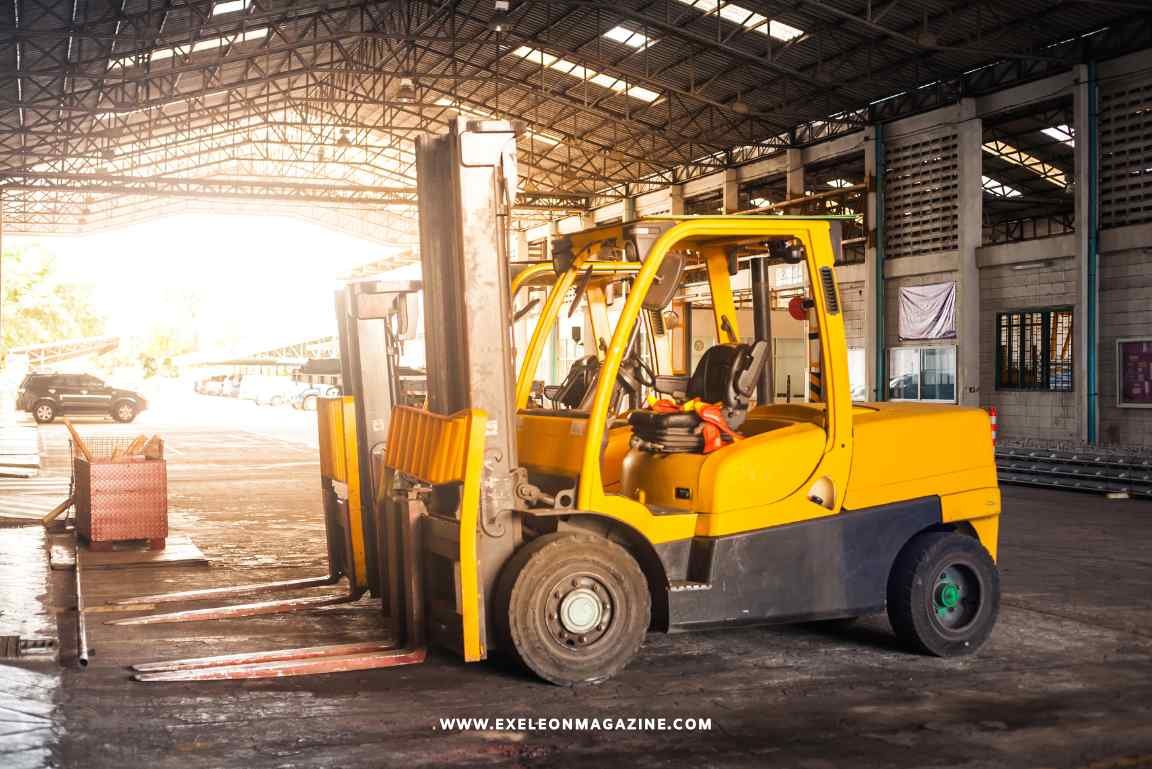
To make operations as safe and efficient as possible, warehouses often make use of various equipment to handle different tasks such as organizing storage, picking orders, or transporting pallets. The type of equipment used can also vary depending on multiple factors. For instance, e-commerce or retail warehouses will most likely need an order picker because their operations require picking individual items frequently. Meanwhile, warehouses with narrow aisle configurations might have better use for a reach truck as this equipment is specifically made for such a warehouse layout.
Knowing the differences among commonly used warehouse equipment not only helps business owners use them optimally. This information can also be crucial in determining whether a particular equipment should be purchased or rented. Here are some key differences of common warehouse equipment that you should take note of to determine which is best suited for your warehouse:
- Primary Function
Knowing the core function of various warehouse equipment ensures that you pick the right tools for the job. Order pickers, as their name implies, are specifically for picking individual items or cases from shelving. This makes them ideal for warehouses with high-density storage systems. Meanwhile, forklifts are primarily used for lifting and moving entire pallets or large, heavy loads within a warehouse. Simply put, the former is used to gather needed orders and the latter is more focused on transportation of bulkier cargo.
Other warehouse equipment can also be used for more specialized functions. For instance, towing tractors are designed to pull or tow carts loaded with goods, making them effective for long-distance transport. Pallet trucks, like forklifts, are used to transfer pallets but usually only for short distances only. If you need to lift pallets to high racking systems, then reach trucks are more suitable for the job.
- Height Accessibility
Depending on the height level of the goods to be accessed, you may also require a particular equipment for the task. For instance, order pickers can usually lift up to heights 30 feet or more for item picking. Meanwhile, forklifts are used to lift pallets to moderate heights of around 20 feet. Do note that it doesn’t elevate the operator but only the load.
When it comes to accessing high storage areas, reach trucks have the best height access. On the other hand, towing trucks operate on the ground and thus have no lifting capacity and pallet trucks are limited to lifting pallets a few inches off the ground for transport.
- Load Capacity
The load capacity of warehouse equipment is crucial to determine whether or not it fits your warehouse’s operational needs. Given that they’re designed for picking individual items or small loads, order pickers naturally have lower load capacity. Forklifts are the opposite, boasting large load capacities that enable them to handle heavy lifting around your warehouse.
Compared to forklifts, pallet trucks and reach trucks have lower load capacities, although powered versions may boast slightly higher load limits. Finally, towing tractors are designed to pull several carts or trailers at once. Thus, they are capable of handling heavier loads by default.
- Maneuverability
Your warehouse’s layout can also influence what type of equipment you can use. If your warehouse has narrow aisles, for instance, then order pickers are more ideal for easier navigation due to their compact size. Similarly, reach trucks and pallet trucks are good for navigating narrow aisles and tight spaces. Forklifts, on the other hand, are more ideal for open areas and standard-width aisles. The same goes for towing tractors, as their towing function requires flat, open floors and wide aisles.
- Operator Involvement
Different types of equipment also require different levels of involvement from its operator. Both order pickers and forklifts need hands-on operations. Order picker operators manually pick and handle items while being elevated, making their jobs more labour-intensive but also more precise for order fulfillment. Meanwhile, forklift operators focus on controlling the machine to lift and position items. Reach trucks, pallet trucks, and tow tractors require the same level of operator involvement as forklifts, meaning that humans primarily drive or control the machine as it does the work.
Purchase or Rent?
By knowing these key differences among common warehouse equipment, you can better evaluate how frequently and critically the equipment will be suitable for your operations. If the equipment will be crucial for daily tasks or long-term efficiency such as getting forklifts to handle heavy-duty lifting in your warehouse, then purchasing may be more cost-effective. For occasional or project-based needs such as requiring reach trucks for seasonal inventory spikes, renting works well enough to save costs while providing flexibility. Understanding specific applications of these warehouse equipment ensures that investments align with operational demands and budget considerations.
Whether you’re looking to purchase new equipment or to rent one for your warehouse, make sure to research their capabilities and ideal uses first to determine whether they’re the right fit for your operations. Let this article be your starting point on learning more about what various warehouse equipment are capable of, so that you can make a more informed decision on whether to purchase or rent them in the future.