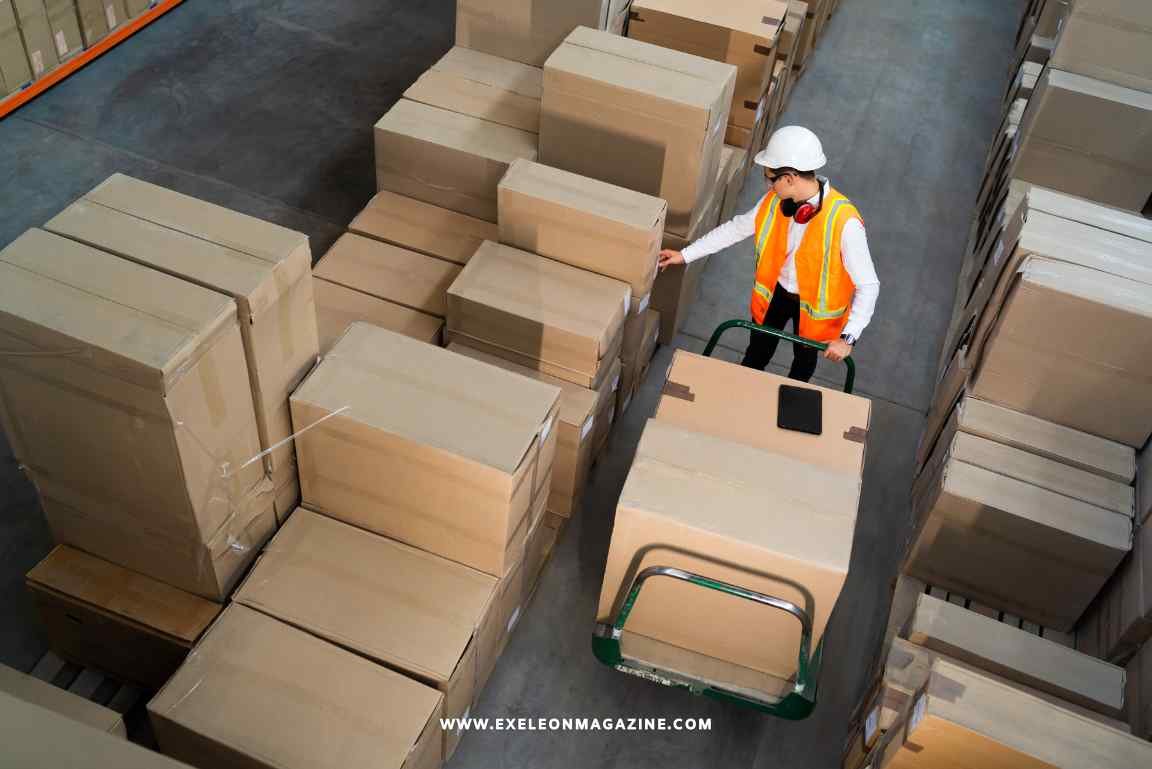
Planning for Increased Demand
Forecasting and planning are the most preparatory steps involved in peak season logistics. Companies need to analyze past trends in order to anticipate demand patterns and understand where bottlenecks might occur. This helps them put in place the right resources, whether it is staff or inventory, to serve customers. Furthermore, this involves coordination with suppliers and shipping partners to ensure a smooth supply chain during this period.
Another important aspect of planning involves incorporating flexibility into the operations of logistics. Peak seasons are always associated with surprises, such as sudden surges in orders or delays in transportation. Contingency plans and a buffer of inventory or resources will help a business address these issues immediately. This proactive approach minimizes disruptions and ensures that customers receive their orders on time.
Optimizing Warehouse Operations
Efficient warehouse management forms the backbone of peak season logistics management. It starts with properly organizing the warehouse for topmost space utilization and easy access. This reduces pick-and-pack time, which is so crucial when volumes are high. Automation tools such as barcode scanners or conveyor belts will further enhance the efficiency and accuracy of the operation.
Training staff to cope with the pressures of peak season is another critical area. Staff should be well-briefed on the systems and processes that will be in place to ensure that operations are seamless. Cross-training of staff for various roles provides flexibility, enabling the team to adjust to fluctuating demands. A prepared workforce greatly contributes to maintaining quality standards, even under pressure.
Strengthening Partnerships with Carriers
Strong relationships with shipping and delivery partners are critical in peak seasons. Businesses should communicate their expectations and volume forecasts to carriers well in advance. This will help the carriers to plan their resources to minimize delays. Just as important is the selection of partners who have a history of reliability during peak periods to ensure consistent service.
Besides partnering with the carriers, the businesses should have diversified options for shipment. Dependency on one carrier exposes them to delay or capacity issues; hence, a business dealing with various providers will ensure that flexibility is maintained and shipment load distributed appropriately. Such an approach not only limits the risks but also assures customers of reliable delivery options.
Maintaining Transparency with Customers
It is very important that there be clear and transparent communication with customers during the peak season. The business should ensure that customers have correct information regarding the timeline for delivery, including any delays. Accurate expectations from the start minimize frustration and help gain trust with customers. Employing real-time tracking also keeps customers informed about their order status, improving the overall customer experience.
When problems do occur, timely solutions are paramount. Companies need to have a system set up for customer service to answer inquiries and offer solutions. They can compensate by giving customers discounts or free shipping for the next orders. Handling the delay with a customer-centric approach helps the company stay reputable even in time troubles.
Leveraging Technology and Data
Technology plays a vital role in smoothing out the logistics in peak seasons. Advanced software solutions can help an organization track its inventory, trace shipments, and predict demand. These tools provide valuable insights to make better decisions and smoothen operations. Automation, such as robotic picking systems or AI-driven logistics platforms, further enhances efficiency and reduces the risk of errors.
The second powerful tool that helps with peak season logistics management is data analytics. By studying the trend and performance indicators, companies can identify certain areas of improvement and can make strategy adjustments accordingly. Continuous monitoring keeps the logistics operation agile, responsive to change in demands, and ready to sustain quality throughout the season.
Continuous Improvement
After the peak period, it is time to carefully analyze the logistics performance of a business. Successes and challenges are identified for better insights into future planning. Feedback from staff, suppliers, and customers also helps to identify areas for improvement. This reflective process ensures that businesses are better prepared for the next peak season.
Investing in long-term improvements, such as infrastructure upgrades or process refinement, strengthens operations throughout the year. Continuous improvement not only enhances efficiency but also ensures that businesses can consistently deliver high-quality service, regardless of seasonal fluctuations.
Peak season logistics can be demanding, but businesses can rise to the challenge with careful planning and execution. Efficiency, communication, and the ability to adapt will go a long way in helping businesses run smoothly while meeting customer expectations. This proactive approach not only safeguards quality during the busy season but also positions the business for sustained success.