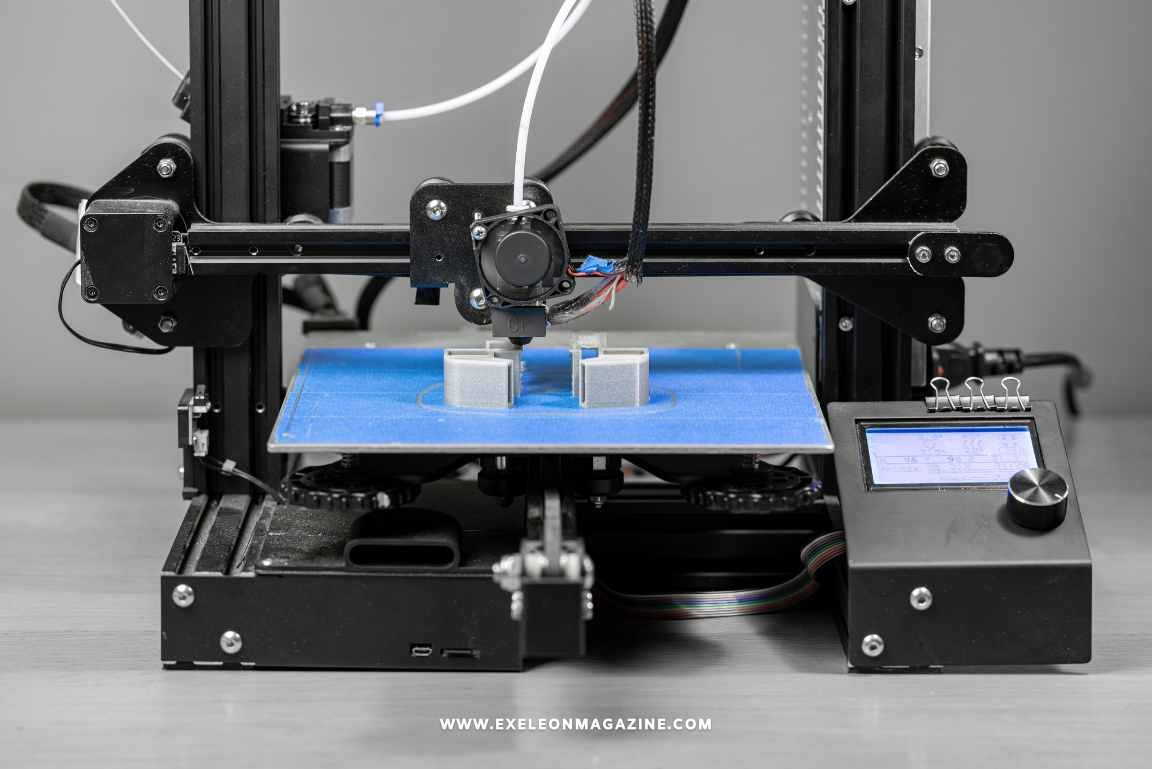
Over the past few years, 3D printing has brought about significant changes in various sectors. 3D printing offers a cost-effective and time-saving option for both prototyping and production. Various industries, including automotive and healthcare, have adopted this technology in the recent past to maintain an edge in their respective markets.
3D printers can also be a fun addition to a home environment. They are fun to work with and an excellent way to unleash your creativity. If you’re looking to buy 3D printers, there are many options to consider. In this article, we delve into the realm of 3D printing and examine its impact on prototyping and production processes. We’ll explore its advantages, applications, hurdles faced and the possibilities it holds for the future.
The Benefits of 3D Printing
A prominent advantage of using 3D printers lies in their ability to produce designs with precise specifications swiftly. Unlike manufacturing techniques that rely on moulds or tools, which can take considerable time to create. 3D printing allows for the digital modelling of complex designs that can be printed within hours or days, significantly reducing production lead times.
Furthermore, additive manufacturing through 3D printing enables a whole new level of customization. Manufacturers now have the flexibility to develop products or modify existing designs without incurring extra costs. This flexibility has created opportunities for niche markets seeking tailored solutions that were previously inaccessible through manufacturing methods.
Industries Embracing Printing
The adaptability of 3D printers has led to their use in a number of sectors. In the aviation and aerospace industries, engineers are now able to craft lightweight aircraft components using advanced materials such as carbon fiber-reinforced polymers. This not only enhances fuel efficiency but also maintains the structural integrity of the aircraft, a task that was once considered technically demanding and financially burdensome.
Moreover, the field of medicine has seen benefits from advancements in printing technology. Tailor-made 3D-printed prosthetics ensure a snug fit for patients while reducing costs compared to other options. Furthermore, surgeons can now produce personalized models based on patient anatomy prior to surgeries, enabling them to thoroughly study the intricacies before entering the operating room.
Overcoming Obstacles
Despite its advantages, transitioning from prototyping to full-scale production with 3D printing comes with challenges that manufacturers must address.
One key challenge is the scalability of 3D printers when it comes to production. While these printers excel in small-batch manufacturing, their efficiency and cost-effectiveness decrease as production volumes rise. For large-scale manufacturing needs, traditional methods may still offer efficiency.
Additionally, sourcing skilled professionals proficient in both 3D designing and operating 3D printers can pose difficulties for companies looking to adopt this technology. In order to boost productivity and reduce mistakes, employees should undergo training that is tailored to the technology they will be working with. Some companies may have concerns about how these technological advancements contribute to growth.
The Future of 3D Printing
Looking ahead at the future of printing, experts in the industry anticipate progress in technology in the upcoming years. Scientists are researching materials that offer improved properties like enhanced strength or conductivity to be used in 3D printing projects. In the near future, manufacturers will also see advantages from upgraded software tools that enable accuracy and smoother workflow management.
Moreover, innovations in metal manufacturing using high-resolution printers are expected to revolutionize industries that require metal parts, such as jewelry or car components. As the technology evolves and becomes more cost-effective, it shows potential for adoption not only among large corporations but also among small and medium-sized businesses.
Sustainability and Waste Reduction
When it comes to sustainability and waste reduction, 3D printing offers a significant advantage. Unlike traditional manufacturing methods, where excess materials are often discarded during production, 3D printers use the necessary amount of material for each print job. This leads to very little waste generation and promotes an environmentally friendly approach to manufacturing.
Furthermore, the capability to create designs with minimal material usage further minimizes the environmental impact. 3D printing allows manufacturers to enhance product designs for resource utilization, minimizing material usage and energy consumption in the production process.
To Conclude
The impact of 3D printing on manufacturing is evident in its ability to facilitate prototyping and customization while lowering costs compared to other methods. Despite obstacles such as scalability and the need for operators, gradual progress leads towards the adaptability of these highly sought-after technologies in various sectors, especially when swiftly piloted recommendations are embraced despite lingering regulatory challenges. The tangible benefits over existing practices signal a future where additive manufacturing becomes a tool in every manufacturer’s arsenal. These advancements will undoubtedly broaden the functionalities of 3D printers, opening up possibilities across industries that are yet to be fully explored.
You May Also Like: