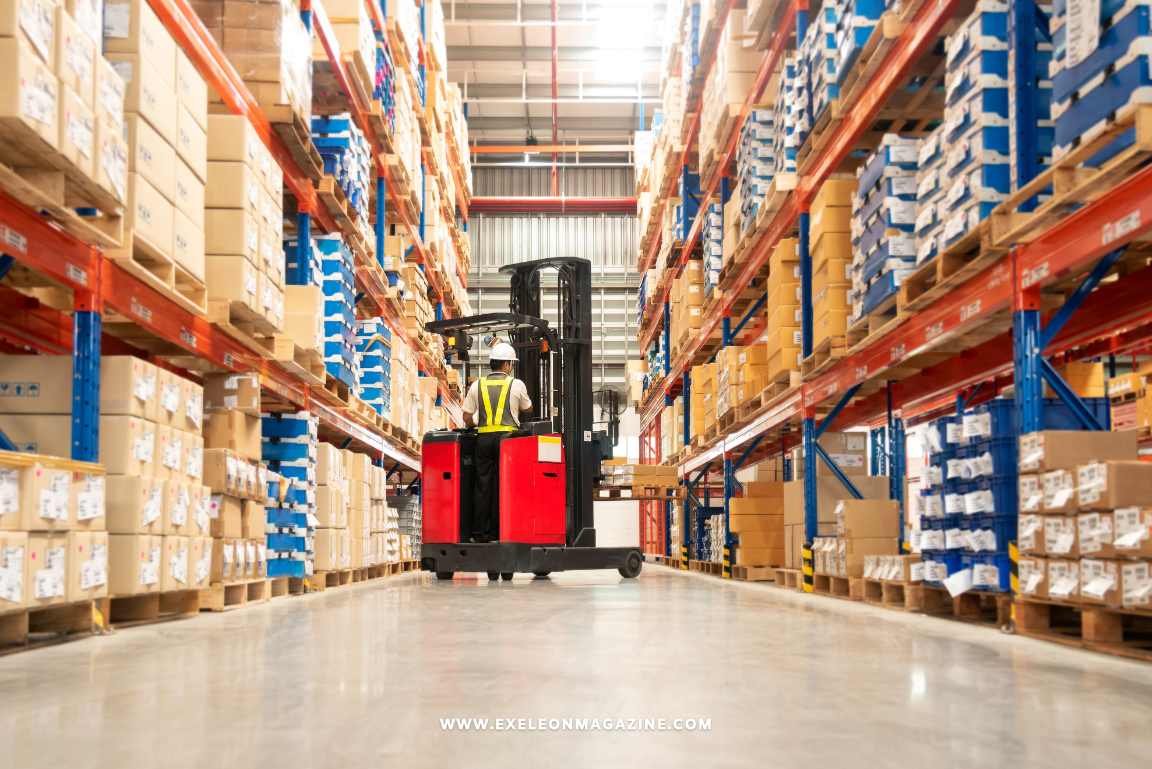
One of the most common and potentially damaging mistakes that business owners and project managers can make is to focus on cutting costs above all else. It seems like this is the best way to operate. After all, lower costs means that your profit margins are higher. If you’re able to work more quickly as well, all the better.
But if you sacrifice quality to reduce costs, you will find that you end up spending more in the long run to patch up any mistakes. This is painfully true when it comes to building projects, especially if you’re trying to expand your business premises.
Low quality work will reflect on your company, and it can come with added costs further down the road as you need to repair or replace different components.
Quality Materials
One thing to consider is the literal building blocks of your project, which is the materials used to create it. No, you don’t need luxury materials everywhere, although a touch of luxury in the right places can have a great impact on how people view your company.
But you do need to think about things like structural steel for storage building construction. This material is easy to work with and will stand the test of time. When you’re creating a warehouse or storage structure, you need to know that your stored goods will be safe from adverse weather conditions and wear and tear.
Good materials can make or break your project and will heavily inform the end result. Think about what you’re building and what you need it to achieve.
Quality Equipment
As well as the materials you use, you also need the right equipment for your project to be successful. You can have all the steel beams you like, but if you have no way to put them in place, your building isn’t going to go anywhere.
When planning your project, think about the equipment you need for each stage. This will allow you to save time and money as you will have the equipment ready to go when you need it, rather than scrambling to find it too late or hiring or buying equipment your workers will never actually use.
For example, when building and stocking your warehouse, you might invest in forklifts to transport building materials and, later down the road, goods for your warehouse. When buying equipment, think about what will be most useful.
Quality Training
Finally, this isn’t the time to skimp on training costs for your contractors. Make sure that they are well qualified and experienced for the job at hand. If you’re managing the project yourself, it’s good to know the people on site.
Think about whether they’re trained for the equipment they will need to use. You will also need to make sure that they are aware of the safety guidelines when on site and that at least one person can do first aid. This way, any accidents are less likely to happen and will be less disruptive to the project.