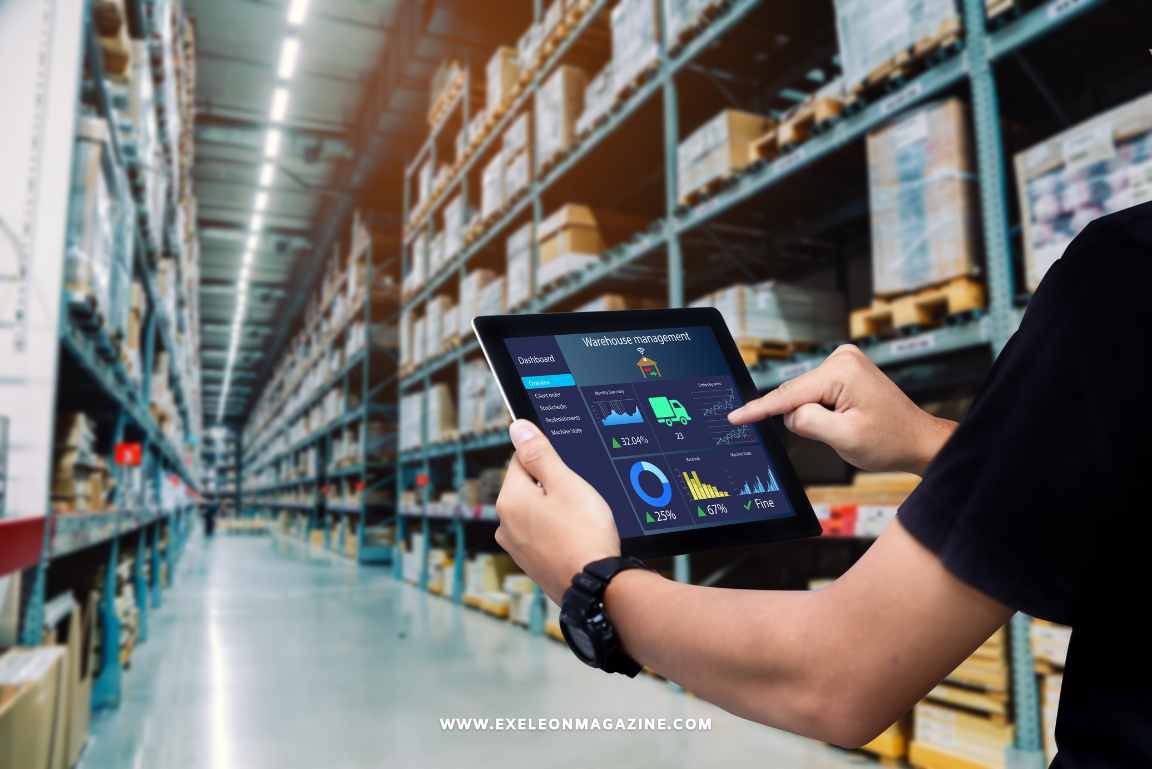
Warehouses are expensive to run and manage effectively, with construction costs as high as $200 to $280 per square foot. However, their need is higher than ever due to today’s complex supply chains. With competition at an all-time high, warehouses must evolve quickly to cater to changing consumer demands. Streamlining operations is the only way to be flexible and save money simultaneously. This article explores four practices you can adapt to do so:
Optimize the Layout
The design of your warehouse must be logical to allow maximum movement in minimum time. Firstly, create clear zones for receiving, storage, and shipping. This will ensure that there is no congestion, hence reducing workers’ travel time. Organize the space so that high-demand items are placed closer to packing stations, saving retrieval time.
Additionally, leave some room for temporary staging areas. These will give you flexibility, helping in times of demand spikes. Design your aisles to allow quick navigation; there must be a practical flow from receiving to shipping so there is no backtracking.
Invest in Automated Material Handling Systems
Invest in conveyors, sorters, and robots. Automating repetitive tasks frees up your employees’ time, enhancing productivity. Productivity gains will likely improve alongside employee motivation since they won’t have to perform repetitive tasks.
You will also benefit from the increase in employee creativity. Workers can focus on complex operations without the burden of tedious tasks, improving their performance. In addition, warehouse robots can autonomously pick, transport, and restock inventory. Consequently, the physical strain on workers will be reduced, speeding up workflows and increasing efficiency.
Install Warehouse Management Software
Investing in warehouse management software (WMS) is the way to go if you wish to optimize inventory management. A robust WMS will help you monitor inventory levels and maximize stock replenishment. It has automated order processing, dynamic inventory tracking, and demand forecasting features. These ensure your stock levels are consistently precise; you will not overstock or understock.
You can integrate this with enterprise resource planning (ERP) systems to take it a step further. This will allow you to gain tighter control over the whole supply chain. WMS will also show you optimal picking routes based on order urgency or product availability. As a result, you can improve your space utilization and fulfill your orders faster.
Implement Barcode Scanning and RFID Technology
Barcode scanning systems use barcodes to scan your data automatically. Manual data entry will no longer be needed, reducing the risk of human error. You can speed up your inventory management process; there won’t be any back-and-forth trying to fix mistakes. Tracking product movements in this way will also minimize stock inaccuracies.
RFID technology will help you keep track of tagged objects, as it offers greater visibility than barcodes. RFID will provide real-time data if your stock needs to be verified or relocated. Your inventory counts will be quicker and more accurate, and the need for manual checks will decrease significantly. It will streamline order-picking by providing instant information on locations and stock levels, increasing profitability.
Endnote
There is no room for inefficiency if you are a company operating in today’s complex business landscape. Streamlining warehouse operations can reduce costs and deliver improved services to your customers. Follow the abovementioned practices and allow your warehouse operations to give you a competitive advantage, driving growth and success.